Extension springs, often composed of metal or other alloys, are common components in a variety of industrial applications, and their application and installation is widely understood.
But what about elastic extension springs? They are typically made from synthetics such as rubber or latex. Their unique properties make them ideal for providing controlled tension, shock absorption, and linear extension. The difference in their construction and application might cause some confusion as to how to safely and efficiently install this innovative component.
To fully benefit from the capabilities of elastic extension springs and ensure the safety of your operations, it’s crucial to install them correctly. In this blog post, we’ll explore the importance of proper installation and offer some tips to help you do it right.
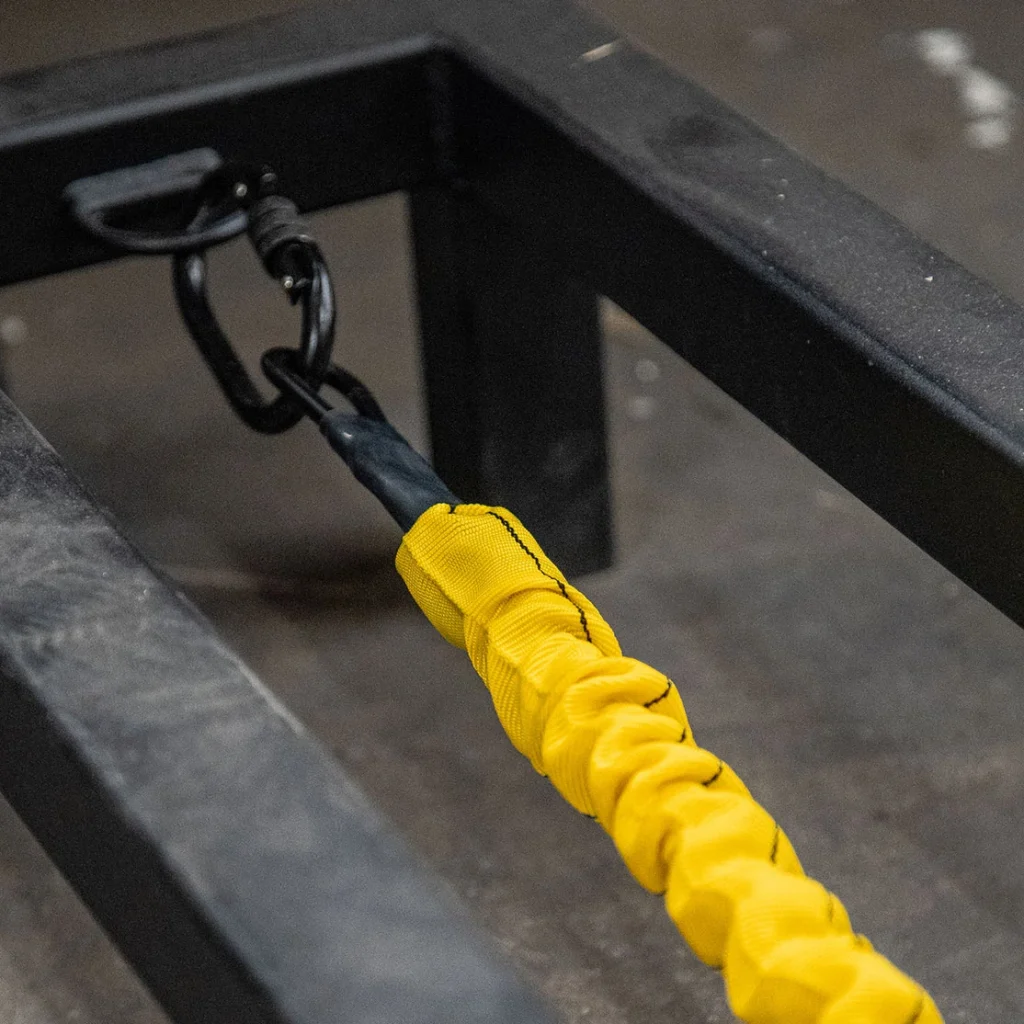
Best Practices
1. Choose the Right Spring for the Job—Before installation, it’s essential to select the appropriate elastic extension spring for your specific application. Consider factors such as load requirements, extension distance, and environmental conditions. Choosing the right spring ensures optimal performance and longevity.
2. Inspect for Damage—Before installation, carefully inspect the spring for any signs of damage, including cracks, deformities, or wear. Damaged springs should never be installed, as they can fail under load, posing safety risks.
3. Measure and Calculate—Accurate measurements are critical. Measure the distance between the attachment points where the spring will be installed. Additionally, calculate the required spring force (tension) based on your application’s needs. This information will guide your installation process.
4. Secure Attachment Points—Ensure that the attachment points, where the spring will be anchored, are strong and secure. Weak or unstable attachment points can lead to spring failure and potential hazards. Use appropriate hardware and reinforcement if necessary.
5. Pre-Tensioning—Some elastic extension springs may require pre-tensioning before installation. Follow the manufacturer’s guidelines for this step, as it can affect the spring’s performance and lifespan.
6. Proper Alignment—Align the spring properly with the attachment points and ensure that it sits evenly. Misalignment can lead to uneven loading, premature wear, and compromised safety.
7. Use Safety Measures—Always wear appropriate personal protective equipment (PPE) when handling and installing springs. Safety glasses, gloves, and other protective gear can prevent injuries.
8. Controlled Release—When installing elastic extension springs, exercise caution during the release process. Release the spring’s tension gradually and in a controlled manner to prevent sudden movements or spring recoil, which can be hazardous.
9. Regular Inspection—After installation, conduct regular inspections to monitor the spring’s condition. Look for signs of wear, fatigue, or any issues that may affect its performance. Replace worn or damaged springs promptly.
10. Follow Manufacturer’s Guidelines—Finally, adhere to the manufacturer’s guidelines and recommendations for installation. Manufacturers provide specific instructions for each type of elastic extension spring to ensure safe and effective installation.
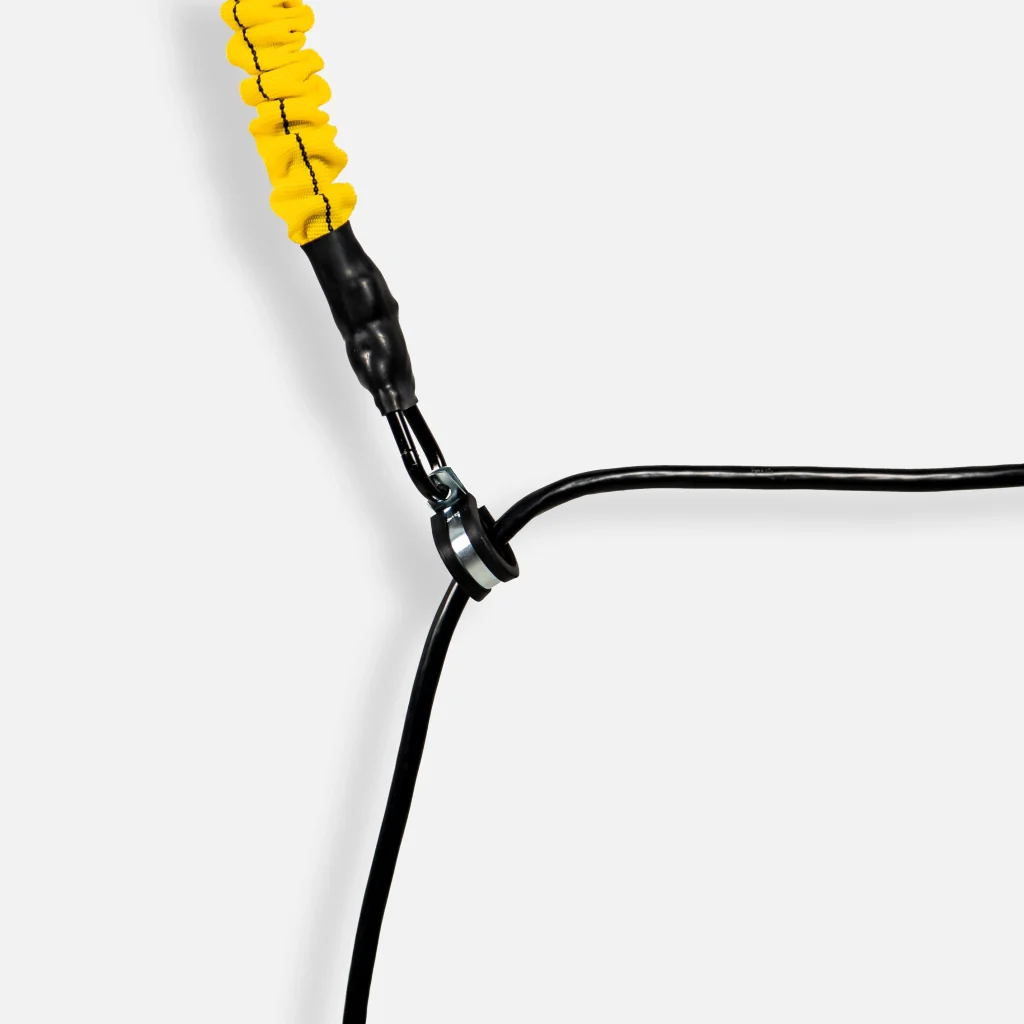
Wrapping It Up
Proper installation of elastic extension springs is paramount for safety and optimal performance. Whether you’re using these springs in automotive applications, industrial machinery, or any other field, following the right procedures and taking safety precautions can prevent accidents and extend the lifespan of your springs. Remember that when it comes to safety, there’s no room for shortcuts.
Follow our blog for more helpful tips on how elastic extension springs can benefit your workspace. For even more helpful information, check out our resources.